In commercial brewing — as with other food, chemical, or industrial processes — control over steam heating can have significant influence on process costs and consistent quality in the final product. But its measurement and control can also be impacted by unique circumstances of those applications. Here is how changing just one aspect of steam measurement brought economy and consistency to multiple aspects of a brewer’s overall process.

The Importance Of Adhering To The Process
In general, having uninterrupted, accurate steam measurement can make noticeable differences in the viability of specific processes and other facets of business operations:
- Steam Costs. With energy use being such a huge factor in so many industries, having pinpoint control over steam measurement can minimize excessive consumption and its associated costs.
- Process Efficiency. Retrofitting existing temperature-critical applications with the addition of a compact drop-in meter unit can refine steam measurement and control to improve process efficiency and consistency without extensive capital investment — even in space-constrained applications.
- Product Quality. The volume, timing, and consistency of steam delivery can impact the quality and consistency of the final product. Problems can manifest themselves as noticeable differences in physical composition or taste related to inconsistent steam heating.
Each industrial process can have its own unique demands that impact the rate and volume of steam required and the way in which it is measured. As with other gas or liquid process line measurements, steam piping’s size, shape, and constrictions/restrictions can impact the accuracy of a meter’s output. Paying attention to such influences can lead to better, more accurate, and more cost-effective meter selection.
In food and beverage applications, however, deviations in precise steam measurement can do more than just impact production costs and profit margins. Resulting inconsistencies that influence the taste or texture of a product can actually damage consumer perceptions and brand reputations. In the brewing industry specifically, the acquisition of smaller, older brewing operations with existing structural limitations can create challenges for global brewing companies trying to standardize on a common process or equipment layout at all their breweries.
Escaping A Vortex Of Brewing Problems
Brewing beer is a prime example of how steam measurement can impact production conditions. In the following example, a brewery switching from vortex meters to V-Cone differential pressure (DP) meters (Figure 1) benefitted from the opportunity to refine steam measurement and provide more finite control over its wort boiling process. This steam calculator demonstrates just how large the annual benefits can be, based on user-supplied variables for pressure, line size, and flow rate.
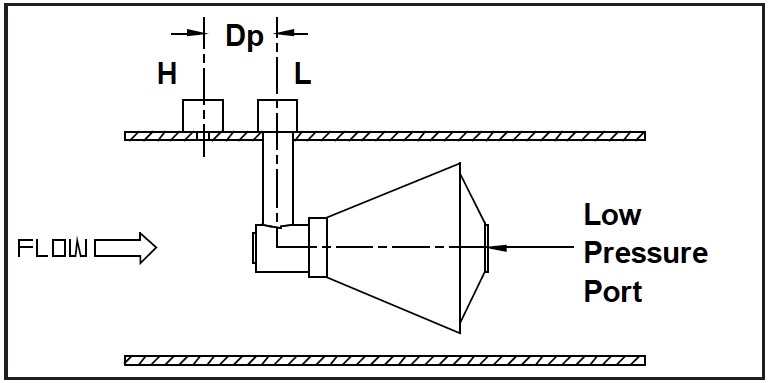
Figure 1. A V-Cone DP meter compares the differential between the high-pressure flow (H) before the cone and the low-pressure port opening (L) on the back of the cone. Because the cone forces turbulent flow out to the periphery of the pipe, the meter is unaffected by turbulence generated from turns or obstructions located immediately upstream of the meter.
Accurate temperature control is a critical goal for any wort boiling kettle, since it is a sensitive process and one of the most energy-intensive aspects of beer production. In this case, the kettle is a large vat with tubing coiled around the exterior wall. The tubing carries a mix of steam and water to heat the wort in the kettle. Modulating the proportion of steam vs. water in the tubing enables the brewery to control the thermal transfer profile of the batch process.
The wort boiling process demands a high volume of steam in its initial phase, enough to bring the large batch up to temperature quickly but without burning the wort at points of direct heat transfer. Once the entire contents of the wort kettle reach a boil, a much lower rate of steam feed can then be used to maintain a desirable temperature for the remainder of the heating cycle.
Variability in steam demand across the approximately 12-hour process — plus the fact that the accuracy of the previously installed vortex meter suffered when running at extremely high or extremely low flow rates — exacerbated the difficulties of steam measurement. Inaccuracy at the high flow rate needed to bring the wort boiling kettle up to temperature could cause overconsumption of steam and even result in some burning of the wort. Also, once the wort kettle achieved a full boil, inaccurate readings from the vortex meter often resulted in cyclical overshooting/undershooting of the ideal steam flow rate as the system tried to maintain a consistent temperature. This was particularly troublesome at the lower flow rates (< 300 m3/hr) demanded for about half of the total heating cycle. Unfortunately, at those flow rates, eddies and irregularities in flow through the vortex meter caused the resulting calculation to become inaccurate. Even as some unknown volume of steam was still getting through, the meter often registered zero flow. When that happened, the brewery was forced to manage the process by instinct.
The same vortex meters had performed appropriately in larger brewery installations having sufficient lengths of straight-run piping but could not generate accurate readings at low flows in a more condensed environment crowded with fittings and tight turns. Turbulence created by the tight piping configuration contributed to occasional loss of readings. The dropout of those readings left the brewery with a blind spot in the control of their heating process.
Since steam is a gas whose volume is affected by temperature and pressure, the raw flow readings from the vortex meter required separate compensation calculations to be interpreted accurately. In this case, separate inputs from the vortex meter, a resistance temperature detector (RTD), and a pressure transmitter all feed into an algorithm in the digital control system (DCS), where the compensating calculations are performed.
By contrast, the replacement V-Cone meter included differential pressure, temperature compensation, and pressure compensation in one unit, so it could calculate and transmit accurate readings even at low flow. The unit in turn provided a temperature-compensated and pressure-compensated 4-20 mA signal to the DCS system. It used two DP cells — one focused on the low range (0 to 50 percent) and one on the high range (51 to 100 percent) — to deliver + 0.5 percent accuracy from zero to full scale (10,000 m3/hr) with turndown ratios as high as 50:1.
Favorable Performance, Favorable Outcomes
Once the V-Cone concept was proved at the first brewery, it was then rolled out to similar applications at several related breweries. The practical outcomes gained from switching to the V-Cone meter (Figure 2) provided the brewer with multiple benefits:
- The high turndown ratio on the V-Cone operation lets the brewer maintain precise readings at high temperatures to bring the wort to a boil and constantly refine the simmer to maintain a lower temperature toward the end of the cycle.
- Knowing the correlation of steam volume to process temperature provided a more timely understanding of the heating process, without delays that can be introduced by direct temperature sensing methods.
- The breweries experienced an average 40 percent reduction in steam consumption derived from the fact that they:
- were not running the boilers unfettered at maximum heat to start the process,
- were not overrunning targeted boil temperatures in the middle of the process, and
- were able to use proportional integral derivative (PID) control to sustain a lower but more consistent cooking temperature after the initial boil.
- A totalizer on each V-Cone package collected analog readings at user-directed intervals and wrote those readings to digital files for process monitoring and subsequent analysis.
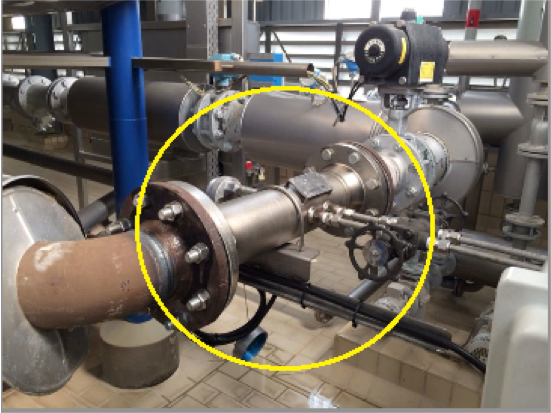
Photo courtesy of McCrometer
Figure 2. The V-Cone meter circled in this photo eliminates the need for extended straight pipe length requirements upstream and downstream of the meter. The previously used vortex meter still visible in the background had suffered from turbulence caused by the lack of sufficient straight-run piping.
Beyond process efficiency, another valuable advantage to global brewing organizations is the ability to maintain a very steady and repeatable process from brewery to brewery, country to country, and continent to continent. Doing so helps them maintain consistent product quality and a clean, crisp flavor for their flagship brands.
How A V-Cone Meter Reduces Compromises
Whether an application involves steam, gas, or a non-viscous liquid in brewing or other industrial processes, the nature of a V-Cone DP meter eliminates many of the limitations of other meter designs. Because the shape of the cone within the pipeline conditions the flow around the periphery of the pipe (Figure 3), it eliminates any pre-existing turbulence in the upstream flow to protect reading accuracy. This makes the V-Cone design an attractive and affordable choice for + 0.5 percent accuracy even in congested piping configurations featuring elbows (single or double), valves, step downs, and other structures that can create havoc for other types of meters. This video demonstrates those V-Cone principles in practice.

Graphic courtesy of McCrometer
Figure 3. The V-Cone centrally located within the pipe reshapes the upstream velocity profile of the steam as it approaches the meter (left), flattening it into the shape of a well-developed profile. The short vortices formed at the back end of the cone (right) create a consistent pressure profile to establish the differential pressure between the flow at the front of the cone and the open port at the back of the cone.
Better Brews, Better Business Results
Whether changing demands are due to organic growth or corporate acquisitions, being able to improve steam measurement and control with a meter that is more compatible to the process enables breweries and other process industries to optimize both product quality and production efficiency. The V-Cone meter’s ability to fit easily into existing infrastructure can also contribute to both improved capital expense (CAPEX) and operating expense (OPEX) spending.
Fitting a V-Cone meter spool piece as short as 18” into an existing piping layout can eliminate the need to expand, move, or replace existing piping infrastructure, with all its attendant CAPEX equipment acquisition and labor costs. In turn, improved steam measurement accuracy not only reduces the OPEX cost of wasted energy consumption, but it can also minimize costs for extra quality control testing or even the dumping of bad batches.
Equally important, providing the information needed to match control of the heating source more closely and more consistently to the dynamics of the process provides greater consistency. That helps to ensure more consistent outcomes that standardize product quality, maintain high customer satisfaction, and reinforce the brand reputation of the manufacturer.