Article | October 6, 2022
Download as a PDF document
Depending on the products being made, many food and beverage processing facilities consume a lot of water. Beyond the actual processing usage, the facilities need water for a variety of utility purposes, including cleaning, heating and cooling systems, irrigation, and more. Decades ago, food and beverage processing facilities were less concerned with the volume of water or steam they were using so long as it didn’t impact production.
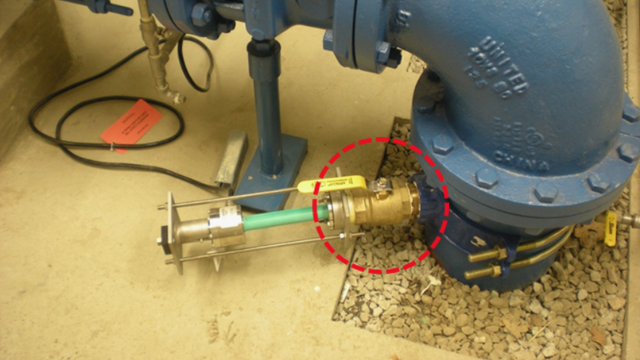
However, as water costs rise and sustainability becomes more front-of-mind, many facilities are urgently trying to measure and manage their utility fluid usage. In the process, they are running into a variety of challenges to reliable and accurate liquid and steam fluid measurement. Below are seven common challenges food and beverage processing facilities face and their potential solutions.
Liquid Measurement Challenges
1. Aging meters. No meter lasts forever. Replacing a full-bore mag meter can be complex and time-consuming. Personnel must stop the pump, drain the system, unbolt the old meter, and bolt the new one into place. The full job can take four to six hours.
A full-profile insertion (FPI) mag meter can be installed in about an hour or two and does not require the removal of the old meter. Because they are hot tapped, they can be installed under full pressure without shutting down the process. If there is an issue with the meter at a future date, it can be removed in just a few minutes. Should it need to be replaced, a new meter can be inserted in its place without having to create a new tapping point. Installing an FPI mag meter means installing a metering point for the life of the facility.
2. No instrumentation where it is needed. Many processing plants either don’t have enough measurement points or don’t have them where they would be most effective. This could be because instrumentation was left out of initial specifications or because of internal changes/reconfigurations. While full-bore mag meters are considered the go-to technology, these devices are difficult to install after the fact. Processes must be stopped, lines must be drained, pipes must be cut, and flanges must be welded before the new meter can be bolted in place.
FPI mag meters solve this problem extremely well for main line sizes above 6” (Figure 1). FPI meters solve the same issues whether the line is 4” or 120” and is certainly more cost effective at the larger line sizes. These meters are hot tapped into place, which requires minimal welding and most importantly can be done while the process is still running. The full-profile sensor measures multiple points across the diameter of the pipe, which accounts for turbulence and allows the meter to take accurate measurements regardless of the amount of or proximity to bends and valves.
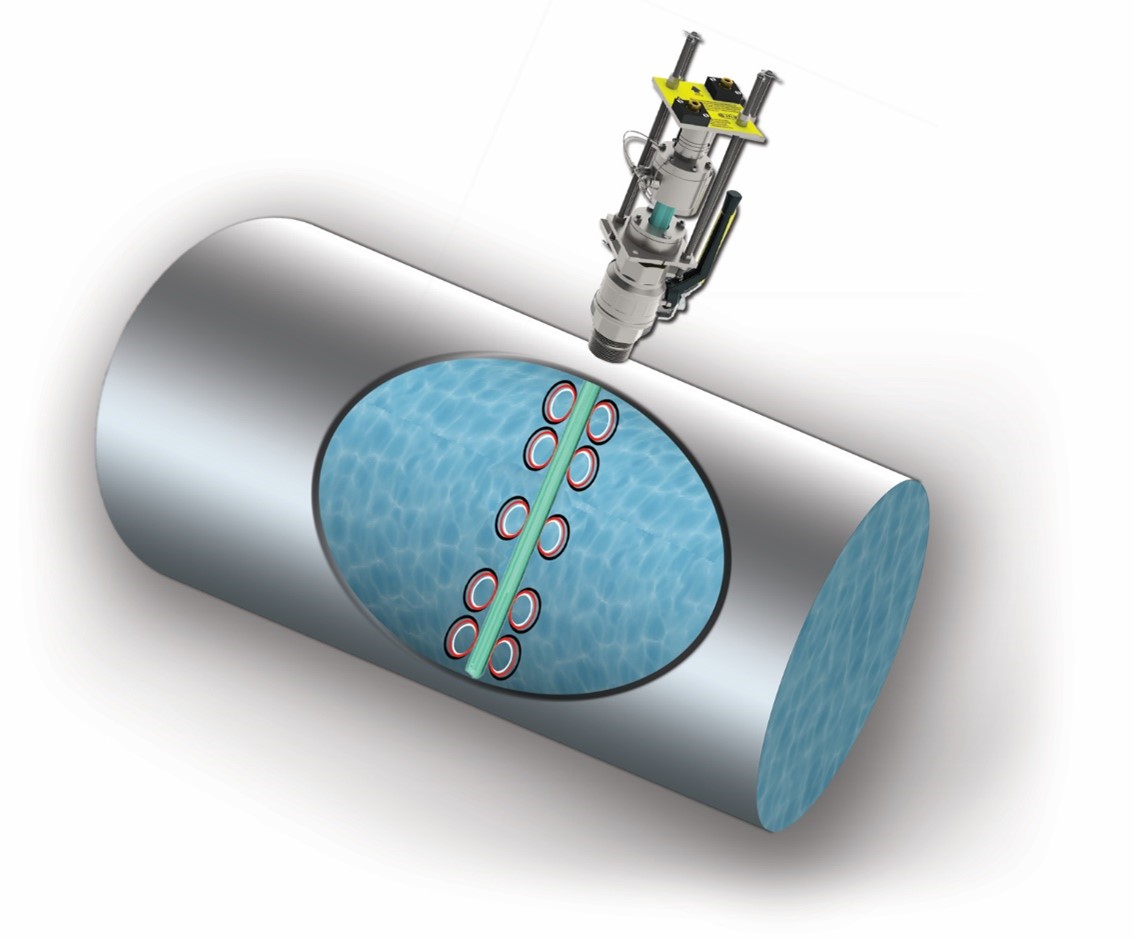
3. Achieving sustainability goals/saving money. When it comes to water usage, sustainability and corporate savings boil down to the same basic challenge: measuring water in compared to water out. Using FPI meters, food and beverage processing plants can measure incoming water with ±0.5% accuracy which is the highest level of accuracy of any hot-tapped meter. The easy hot-tap installation means that these meters can be placed in nearly any location. With enough meters, plants can use data to reduce waste via repaired leaks and discover areas where water can be reused rather than dumped, and more.
Steam Measurement Challenges
4. Long straight pipe requirements. Measuring steam imposes similar but distinct challenges and very different technological solutions. One of those challenges is the need for long straight runs prior to the meter. Orifice plate differential pressure (DP) meters, a decades-old industry standard for steam measurement, requires about 30' of straight pipe. Orifice plates are very sensitive to turbulence, which can cause puddling, inhibiting proper measurement.
V-Cone DP meters resolve this by using a conical shape to push turbulence to the outside of the device (Figure 2). This eliminates the need for long straight runs, allowing the V-Cone to be installed anywhere in the system and still maintain a ±0.5% accuracy.
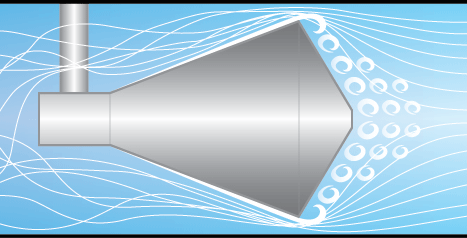
5. Tighter control on low flows. Steam is expensive to make. Unfortunately, orifice plates often fail to read at low flow rates, which can make it difficult to control the amount of steam being used. Another advantage of V-Cones is that they have a sensor opening that is about the size of the inner pipe diameter, which allows it to detect further into the low flow range than orifice plates. Its ±0.5% accuracy further improves the level of control and reduces expensive waste.
6. Too much maintenance. Orifice plate meters must be checked and sometimes replaced every few years. The nature of their design forces the steam over the edge of the plate, which mars the edges and, over time, reduces the effectiveness of the device. V-Cones change the friction dynamic through their conical shape, gently directing the steam to the outside of device, as opposed to presenting a flat obstruction. As such, they are known to last around 25 years without maintenance.
7. Off-the-shelf solutions won’t work. Whether it’s an unusual pipe diameter or another challenge, sometimes a standard solution won’t suit the application. V-Cones can be customized based on specific application needs, including exotic materials, end connections, taps, and more.