Article | November 8, 2022
Download as a PDF document
Accurately measuring the flow of liquid, steam, or gas is often a difficult challenge for engineers who must contend with a hazardous flow environment, multiple pump inputs, and diverse infrastructure conditions.
The cost of installation and maintenance for the piping and structural support that alleviate these issues can be steep — especially when pipe sizes are increased, and space is limited. Users, then, must reduce their accuracy expectations or the reliability of their measurements in order to meet process requirements and project goals.
Differential Pressure Flow Meters Ensure Accuracy, Stability, Flexibility
To ensure accuracy, stability, and installation flexibility, engineers need differential pressure (DP) flow meters that offer versatility and long-term reliability, all while minimizing maintenance and reducing operating costs.
What Is a Differential Pressure Flow Meter?
A differential pressure flow meter is a measurement technology that uses Bernoulli’s principle to measure the flow of liquid, steam, or gas in pipes.
Because Bernoulli’s principle defines the relationship between the velocity of a fluid and the pressure of a fluid, differential pressure meters based on the principle provide more accurate, reliable readings than many alternative devices.
Electromagnetic flow meters (also called mag meters or magnetic flow meters), are volumetric flow meters that use electromagnetic induction to measure liquid velocity.
This method of measurement is highly accurate at measuring water-based fluids as they pass through a pipe.
Mag flow meters do not have any moving parts, so there is minimal need for maintenance or replacement. Accuracy over a wide flow range can be as good as ± 0.5% of flow rate or better.
How Do Differential Pressure Flow Meters Work?
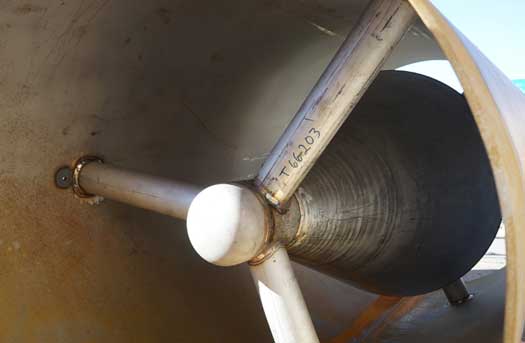
3-gusset V-Cone awaiting shipment
By introducing a constriction or obstruction in the pipe that creates a pressure drop, DP flow meters can precisely measure the flow of fluid within that pipe. As the pipe flow increases, more pressure drop is generated. This provides an almost-immediate response time to any pressure changes, regardless of flow velocity and other characteristics.
Bernoulli’s equation asserts that pressure drop across the constriction is proportional to the square of the flow rate. Pressure sensors can measure the pressure before and after construction, so the flow rate is always accurate.
Elements of Differential Pressure Meters
Elements of Differential Pressure Meters
- Primary element - There are a variety of designs and options that might be considered primary elements of a DP meter. Averaging pitot tubes, an integral flow orifice (IFO), and wedges are all options that may be used based on specific line sizes and flow rates. Engineers must consider the benefits of each (such as greater process control, multiple mounting configurations, ease of installation, maintenance cost, and reduced permanent pressure loss) to determine which primary element they’ll use.
- Secondary element - The differential pressure transmitter for flow measurement is considered the secondary element, and it measures differential pressure flow. In some cases, this element might include a flow computer with temperature and static pressure input.
- Tertiary element - Although not every DP meter includes tertiary elements, advanced systems often do. Gas chromatographs and temperature transmitters are considered tertiary elements.
Benefits of Differential Pressure Meters
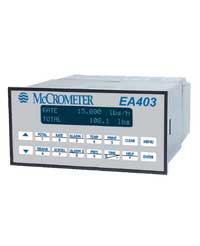
allows for manual access to the measurements
and display settings of the flow meter
and its transmitters
Engineers who rely on differential pressure meters gain a variety of valuable benefits, including:
• More reliable measurements
Differential pressure meters deliver accurate measurements, despite disruptive turbulence and a broad range of flow characteristics. They’re uniquely designed to maintain accuracy and consistency of readings, even in difficult or varied flow conditions.
In fact, McCrometer’s V-Cone DP meter is self-conditioning, which helps it tolerate turbulent flow with minimal to zero straight-run requirements. This is in contrast to other DP meters that require somewhat clean, laminar flow in the line ahead of the flow meter.
• Minimal maintenance
Because some differential pressure flow meters don’t include movable parts, they don’t require the maintenance that’s usually needed for orifice-plate or ultrasonic meter designs
Some don’t even need any recalibration, which means facility managers and other stakeholders don’t have to conduct any routine system maintenance.
• Customizable solutions
There are many key aspects of DP meters that can be fully customized to fit customer requirements, such as turndown, total pressure loss, and valve size for optimized operability.
• Installation flexibility
Some differential pressure meters can be pre-configured based on the specific application (e.g., across filters, backflow preventers, and heat exchangers) and ready to install, which reduces both installation time and costs and improves overall productivity.
• Reduced footprint
DP flow meters are built to fit in a compact space and reduce the amount of piping that leads up to and away from the meter
That means spending less space and money configuring piping and support requirements without sacrificing accuracy. This also reduces any critical space and weight demands for platform-mounted applications.
• Low permanent pressure loss
Since differential pressure meters provide a consistent, even flow around transitions, they ensure less permanent pressure loss.
• Minimal straight-pipe requirements
While alternative meter devices require additional costs for piping and structure support, some DP meters can cut both upstream and downstream pipe requirements.
They offer smooth flow profiles through measurement zones to deliver accurate, reliable readings.
When to Use a Differential Pressure Flow Meter
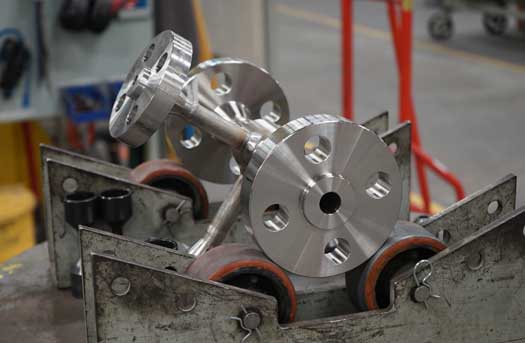
apart to accommodate limited spacing
Engineers usually choose differential pressure meters because of the measuring principle they’re based upon, which is standardized in ISO 5167 and ensures accurate, reliable results.
They also work in both low and high temperature applications, can be used in large pipes, and are easy to maintain. Since DP meters can be made from a variety of materials, they’re suitable for many types of gasses and liquids.
They minimize potential leak sources because they can be welded and offer a low total cost of ownership. Depending on the flow element applied, differential pressure meters can vary in appearance.
Each differential pressure meter type offers distinct benefits:
- Orifice plate- Easy installation and low purchase cost.
- Venturi meter- Low permanent pressure loss, high accuracy of readings.
- Vortex- Quick leak detection and low power consumption.
- Coriolis- Can be used in a wide range of conditions, works for bi-directional flow.
- Cone- Low sensitivity to installation effects, minimal permanent pressure loss, quicker. to install, lower costs, minimal straight-run requirements, works for bi-directional flow.
When NOT to Use a Differential Pressure Flow Meter
When NOT to Use a Differential Pressure Flow Meter
You should choose a different flow measurement method if:
- The volume flow rate is less than 2 liters per hour (l/h).
- The pipes have small diameters (< 0.5”).
- You need to measure without any process interruption.
Featured DP Products
McCrometer offers a suite of four unique products for differential pressure (DP) flow measurements to best serve a variety of applications.
Shop all differential pressure flow meters or learn more about our featured products.